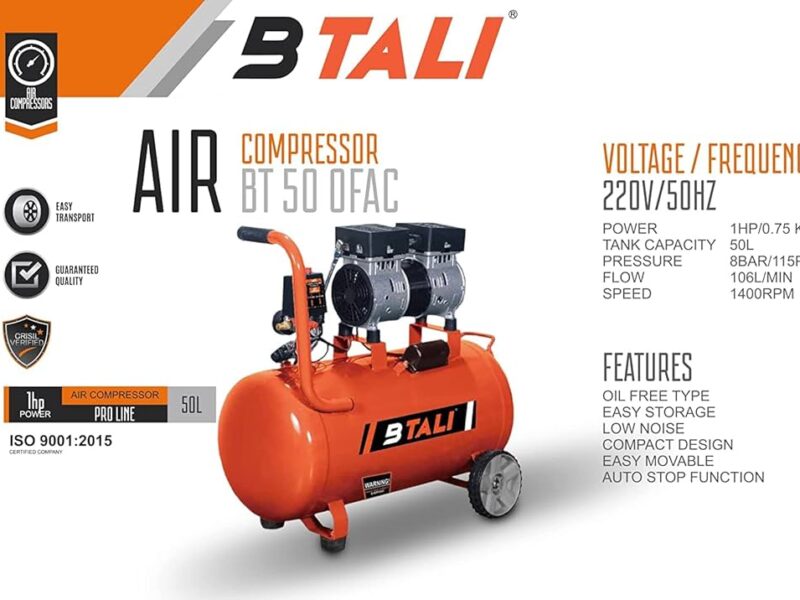
For those seeking a reliable and efficient pressure washer, Btali offers high-quality models designed for both home and car use. Their pressure washers are known for durability, ease of use, and powerful cleaning performance, making them a great choice for Indian consumers.
Air compressors are indispensable tools across various industries and homes, powering everything from pneumatic tools to intricate machinery. However, with a vast array of options available, selecting the right compressor can be daunting. Understanding the types of air compressors and their specific applications is crucial for making an informed decision. This comprehensive guide will delve into the different types of compressors, their working principles, and how to choose the perfect one for your unique requirements.
Understanding the Basics: What is an Air Compressor?
Before exploring the compressors and its types, let’s understand the fundamental principle. An air compressor is a mechanical device that converts power into potential energy stored in pressurized air. This pressurized air is then released to perform various tasks, from inflating tires to powering heavy-duty industrial equipment.
Classifying Air Compressors: A Deep Dive
Air compressors can be broadly classified based on their operating mechanism and application. Here’s a detailed look at the most common types:
1. Reciprocating Compressors:
- Working Principle: These compressors utilize a piston moving within a cylinder to compress air. The piston’s reciprocating motion draws air into the cylinder during the intake stroke and compresses it during the compression stroke.
- Types:
- Single-Stage Reciprocating Compressors: These compressors compress air in a single stroke. They are suitable for light-duty applications like inflating tires, powering small pneumatic tools, and hobbyist projects.
- Two-Stage Reciprocating Compressors: These compressors compress air in two stages, resulting in higher pressure output and improved efficiency. They are ideal for medium to heavy-duty applications like automotive repair shops, construction sites, and industrial settings.
- Advantages: Relatively low cost, simple design, and readily available parts.
- Disadvantages: Can be noisy, produce pulsating airflow, and have higher maintenance requirements compared to other types.
- Applications: Home garages, small workshops, automotive repair, light industrial tasks.
2. Rotary Screw Compressors:
- Working Principle: These compressors use two helical rotors (screws) to compress air. As the rotors rotate, the air is trapped and compressed between the screws and the compressor housing.
- Types:
- Oil-Lubricated Rotary Screw Compressors: These compressors use oil to lubricate the rotors and seal the compression chamber, resulting in higher efficiency and longer lifespan.
- Oil-Free Rotary Screw Compressors: These compressors do not use oil for lubrication, making them suitable for applications where clean, oil-free air is essential, such as food processing and medical industries.
- Advantages: Continuous airflow, quiet operation, high efficiency, and low maintenance requirements.
- Disadvantages: Higher initial cost compared to reciprocating compressors.
- Applications: Industrial manufacturing, large workshops, food processing, medical facilities, and other continuous-duty applications.
3. Centrifugal Compressors:
- Working Principle: These compressors use a rotating impeller to accelerate air and convert kinetic energy into pressure energy. The high-speed rotation of the impeller forces air outward, increasing its velocity and pressure.
- Advantages: High airflow capacity, oil-free operation, and suitable for large-scale industrial applications.
- Disadvantages: High initial cost, complex design, and not suitable for small-scale applications.
- Applications: Large industrial plants, power generation, oil and gas refineries, and other high-volume air compression needs.
4. Axial Compressors:
- Working Principle: These compressors use a series of rotating blades (rotors) and stationary blades (stators) to compress air. The rotors accelerate the air, while the stators convert the kinetic energy into pressure energy.
- Advantages: High airflow capacity and compact design.
- Disadvantages: Complex design, high initial cost, and sensitive to changes in operating conditions.
- Applications: Gas turbines, jet engines, and other high-speed, high-volume air compression applications.
5. Scroll Compressors:
- Working Principle: These compressors use two interleaved spiral-shaped scrolls, one stationary and one orbiting, to compress air. As the orbiting scroll moves, it traps and compresses air pockets between the scrolls.
- Advantages: Quiet operation, oil-free operation, and compact design.
- Disadvantages: Limited pressure output and not suitable for heavy-duty applications.
- Applications: Medical equipment, laboratory applications, and other applications requiring clean, quiet air compression.
6. Piston Compressors (Portable):
- Working Principle: These are smaller, often oil free, and designed for portability. They use piston technology like the larger reciprocating compressors.
- Advantages: Very portable, inexpensive, and good for small jobs.
- Disadvantages: Low duty cycle, noisy, and not designed for constant use.
- Applications: Home use, tire inflation, small air tools, and DIY projects.
Choosing the Right Compressor for Your Needs:
Selecting the appropriate air compressor depends on several factors, including:
- Application: Determine the specific tasks you need the compressor to perform. Light-duty tasks require smaller, less powerful compressors, while heavy-duty industrial applications demand larger, more powerful units.
- Airflow (CFM): Calculate the required airflow in cubic feet per minute (CFM) based on the tools and equipment you plan to use. Ensure the compressor can deliver sufficient CFM to meet your demands.
- Pressure (PSI): Determine the required pressure in pounds per square inch (PSI) based on the tools and equipment you plan to use.
- Duty Cycle: Consider the frequency and duration of compressor usage. Continuous-duty applications require compressors with higher duty cycles.
- Power Source: Choose a compressor with a suitable power source, such as electric, gasoline, or diesel.
- Portability: If portability is essential, opt for a portable compressor with wheels and handles.
- Noise Level: Consider the noise level of the compressor, especially if it will be used in residential or noise-sensitive environments.
- Maintenance: Evaluate the maintenance requirements of the compressor, including oil changes, filter replacements, and other routine tasks.
- Budget: Determine your budget and choose a compressor that offers the best value for your money.
Matching the Compressor to the Job:
- Home Use: For inflating tires, powering small air tools, and DIY projects, a portable or single-stage reciprocating compressor is often sufficient.
- Automotive Repair: For powering pneumatic tools in automotive repair shops, a two-stage reciprocating compressor or a rotary screw compressor is recommended.
- Industrial Manufacturing: For continuous-duty applications in industrial manufacturing, a rotary screw compressor or a centrifugal compressor is ideal.
- Medical and Food Processing: For applications requiring clean, oil-free air, an oil-free rotary screw compressor or a scroll compressor is essential.
- Large Scale Industrial: For the largest of industrial needs, centrifugal and axial compressors are used.
Maintenance and Safety:
Proper maintenance is essential for ensuring the longevity and efficient operation of your air compressor. Follow the manufacturer’s recommendations for routine maintenance tasks, such as oil changes, filter replacements, and air tank draining. Always prioritize safety when operating an air compressor, wearing appropriate safety gear and following safe operating procedures.
Conclusion:
Understanding the types of air compressors and their respective applications is crucial for making an informed decision. By considering your specific needs, airflow requirements, pressure demands, and budget, you can select the perfect compressor to power your projects and applications. By understanding the different types of compressors you will be able to best choose your next compressor. Whether it’s a small portable unit for home use or a large industrial compressor for heavy-duty applications, there’s a compressor to meet your needs. By understanding compressors and its types, you are now prepared to make an informed purchase.